Pumping Station Repair
With the Environment Agency putting more pressure on water authorities to protect the environment from pollution. Newer pumping stations and regular maintenance can drastically reduce the environmental risks associated with overflowing and breakdowns.
Pumping Station Repair:
The importance of maintaining your pumping station:
Unstable weather and growing amounts of development land, increases the importance of a pumping station that is working as it should. This is because pumping stations don’t just take away the waste effluent produced by housing developments.
They are also key in making sure that the sewer system doesn’t become flooded in heavy rain. Many larger pumping stations can store liquids to make sure that this doesn’t happen.
With the Environment Agency putting more pressure on water authorities to protect the environment from pollution. Newer pumping stations and regular maintenance can drastically reduce the environmental risks associated with overflowing and breakdowns.
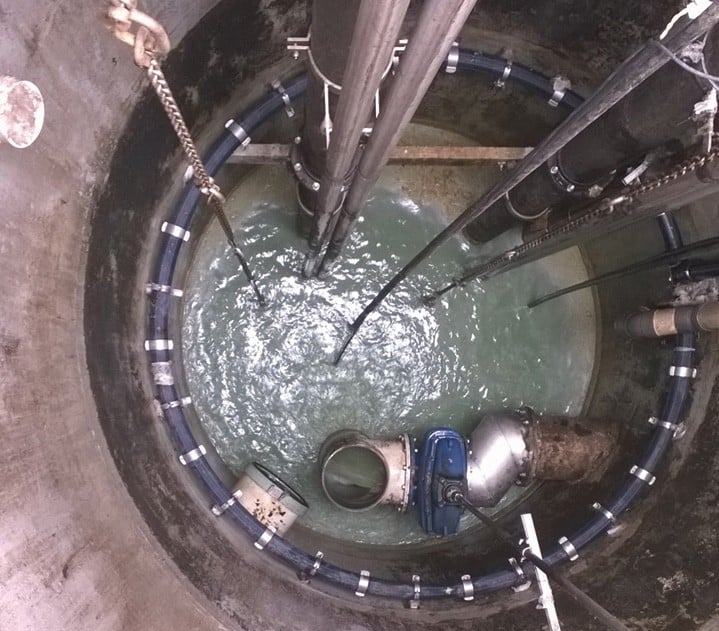
Pumping station repairs: To help keep your property free from drainage disruptions we recommend having a maintenance plan in place.
A pump provides the necessary pressure to move waste up the pipes in your drainage system to the sewer lines. A pump is necessary when the wastewater needs to flow upwards to the other pipes, which would not be possible otherwise. Maintenance is essential to any part of a drainage system and a pump is no different, if a pump fails you may see leaks and an overflow of the wastewater. This would clearly be quite disruptive to a business which is why we recommend having a maintenance plan in place.
Our Pumping Station Maintenance Plans
We work closely with our suppliers to help design and install pumps that fit your home and businesses needs. This means that once the pump is in place our team will have an in-depth knowledge of the site and pump, so that we can tailor a maintenance plan to you. It’s very important to carry out regular pump maintenance to keep them running efficiently.
The regular cleaning and checks can take place at a time that suits you, and we recommend this happens every 3-6 months depending on the size of the pump and the frequency of use. (eg: a highland pump station may need 2-3 interim services a year, whilst a low demand may only require 1 a year).
This regular maintenance is extremely beneficial as it can help identify issues early on before they escalate, thus saving you emergency call outs, fixes and money in the long term.
As part of our maintenance plan our engineers will check for leaks, check the overall condition of the electrical elements, float switches and guide rails to make sure it is operating as it should be. Not having a maintenance plan means you run the risk of blockages and general wear and tear that weakens the pump.
If you do have an issue with your pump station, one of our engineers can be on site as quickly as possible to carry out the inspection and repairs necessary. Identifying the cause is key to ensuring the problem is resolved. Over time, the natural wear and tear of use can mean that parts of the pump will need replacing. Our engineers can quickly resolve these problems and fit the required parts ensuring that your pumping station is running in optimal working condition.
We offer repair and maintenance services across Kent, London and the south of England. All of our engineers are highly trained and fully insured.
Think Pumping Station Repairs: Think The Pump People
Have any questions?
Included in Every Service
Hose or jet-wash the sump-internals/pumps (Note: – a suitable water supply adjacent station to be provided by client.)
Check pumps for any blockages and remove same.
Audibly check motor bearings for noise.
Strip *volutes to expose impellers & seals.
Replenish motor oil as required.*
Check for correct seating of flaps/sealing. Lubricate and refit covers.
Inspect and note any corrosion to pipework/valves within sump.
Carry out ‘megger’ test (insulation resistance test) to motor windings noting any low readings.
Carry out clamp-meter tests noting correct running current of pump motors.
Inspect and note wear to same.
Check discharge stools, guide rails and upper support brackets noting any corrosion.*
General condition – check and report upon the general condition of sump and access opening. * Where applicable
Breakdown crust on surface of water / effluent within sump.
Check for free rotation of impellers/visually check condition of same.
Check condition of motor oil, noting any ‘milky’ appearance indicating mechanical seal failure
Inspect condition of mechanical seals.
Clean and inspect condition of neoprene cabling and glands on pumps and floatswitches.
Rotate and lubricate isolation valves to ensure correct operation.*
Lift floatswitches and check correct auto sequence.
Check any electrical junctions/boxes/connectors. Dry out and re-make/re-seal (as required)
Open control-panel and check for correct movement of motor starter contacts.*
Check all panel bulbs and audible sounders. Report any replacements required.*
Check pump lifting chains, shackles and hooks noting and corrosion.